Imagine uma empresa onde tudo está no seu devido lugar. As ferramentas de trabalho não apenas são organizadas, mas também fáceis de encontrar. O chão está limpo, os processos são otimizados e os colaboradores trabalham de forma fluida, sem interrupções desnecessárias. Parece um sonho utópico? Bem, na verdade, esse é o resultado tangível de uma metodologia chamada 5S, que já foi responsável por transformar ambientes caóticos em verdadeiros exemplos de eficiência e produtividade.
O 5S vai muito além de uma simples organização. Sua essência reside na mudança de mentalidade e cultura dentro das organizações, buscando não só melhorar o ambiente físico, mas também criar um local de trabalho mais saudável, seguro e eficiente.
Como um conjunto de “palavras simples” mudou fábricas inteiras
Quando ouvimos falar de uma metodologia que tem o poder de transformar completamente o ambiente de trabalho e aumentar significativamente a produtividade, é difícil imaginar que ela possa ser resumida em cinco palavras simples. No entanto, o 5S, nascido no Japão no pós-guerra e amplamente utilizado até hoje, é exatamente isso: uma coleção de cinco princípios básicos que trazem impactos profundos na organização e na eficiência. Vamos detalhar cada uma dessas palavras e ver exemplos práticos de como elas têm mudado fábricas e empresas ao redor do mundo.
Seiri (Utilização): Separando o que é útil do que não é
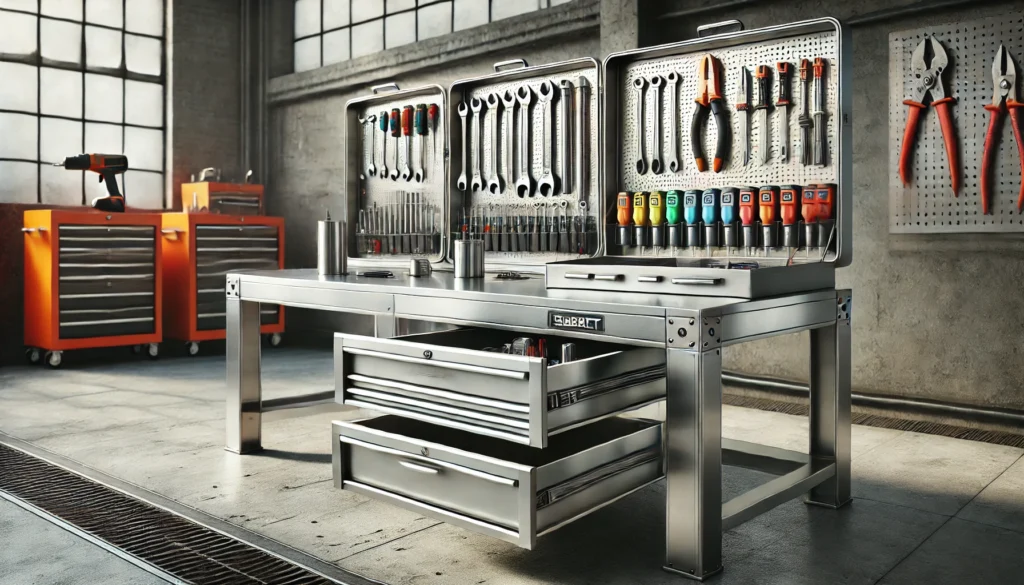
O primeiro passo no 5S é Seiri, que significa “separar”. A ideia aqui é simples, mas incrivelmente poderosa: eliminar tudo que não é necessário. Parece uma tarefa óbvia, mas nas fábricas e escritórios, é comum encontrar ferramentas, equipamentos e até documentos que ocupam espaço e, pior, atrasam processos.
- Exemplo na prática: Imagine uma linha de montagem em uma fábrica de automóveis, como a da Toyota. Inicialmente, a área ao redor das máquinas estava repleta de peças que eram usadas esporadicamente ou que já haviam sido substituídas por novas versões. Após aplicar o Seiri, a Toyota eliminou mais de 25% dos materiais da área de trabalho, permitindo uma circulação mais ágil dos trabalhadores e redução do tempo de busca por peças. Isso economizou cerca de 15 minutos por tarefa em cada etapa da produção, resultando em uma produção mais fluida.
- Outro exemplo: Em um escritório, a Philips usou o Seiri para eliminar documentos físicos que já estavam digitalizados, liberando espaço valioso e acelerando o acesso a informações. O resultado foi uma economia de 12% no tempo de resposta a consultas internas.
Seiton (Organização): Um lugar para cada coisa
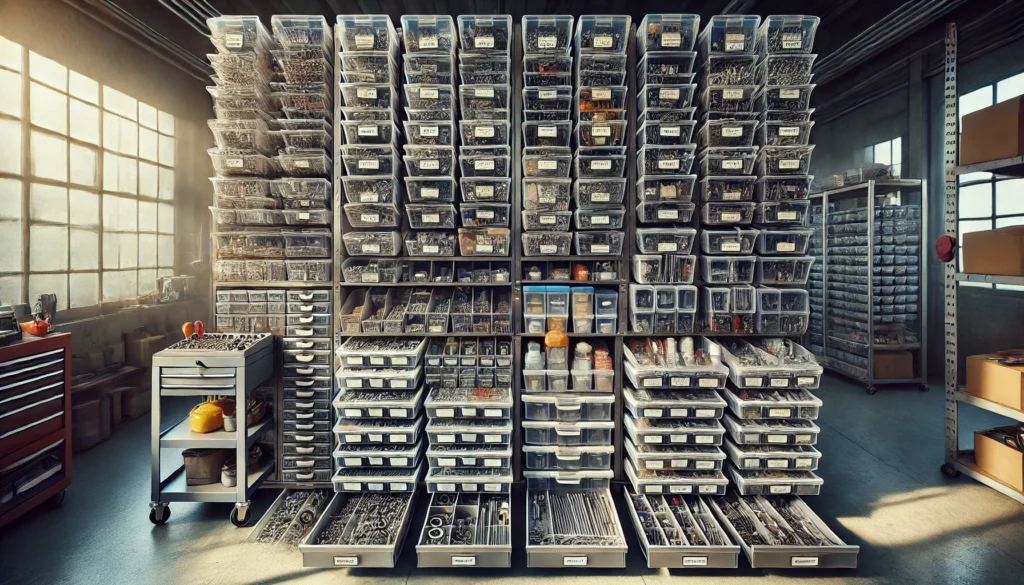
Depois de separar o útil do inútil, chega o momento de organizar o que sobrou. Seiton diz respeito a garantir que tudo tenha um lugar específico e esteja sempre em seu devido lugar. Isso reduz o tempo de procura por ferramentas e melhora a eficiência operacional.
- Exemplo na prática: Na fábrica da Embraer, o Seiton foi aplicado de forma rigorosa. Ferramentas de manutenção, que antes eram distribuídas aleatoriamente entre diferentes caixas de ferramentas, foram organizadas em estantes com compartimentos dedicados e etiquetas claras. Além disso, a Embraer usou cores para destacar áreas de trabalho e tipos de ferramentas, o que reduziu o tempo de busca em mais de 30%. Hoje, o tempo para localizar uma ferramenta essencial foi reduzido de 20 minutos para menos de 5 minutos.
- Outro exemplo: No setor de saúde, o hospital Mount Sinai organizou materiais médicos críticos, como kits de emergência, em locais de fácil acesso e padronizados em toda a instituição. Isso reduziu o tempo de resposta em emergências em 15%, um tempo precioso que pode salvar vidas.
Seiso (Limpeza): Limpeza constante para evitar problemas
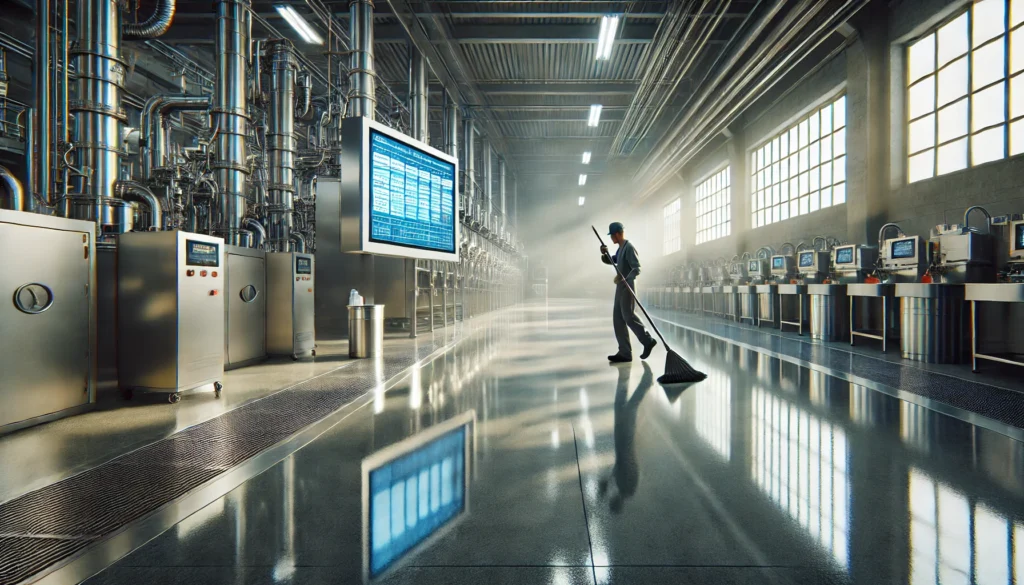
Manter o ambiente de trabalho limpo vai além da estética – é uma questão de eficiência e segurança. Seiso significa “limpar”, e no contexto do 5S, a limpeza é feita de maneira sistemática e contínua. O objetivo não é apenas limpar, mas também evitar que a sujeira ou desorganização voltem a aparecer.
- Exemplo na prática: Na fábrica da Fiat Chrysler, após implementar o Seiso, a equipe começou a realizar limpezas periódicas nas máquinas, não apenas para manter a ordem, mas também para identificar possíveis falhas operacionais. Eles descobriram que máquinas limpas apresentavam 20% menos problemas mecânicos, o que gerou uma economia de milhões em manutenção preventiva.
- Outro exemplo: Na indústria alimentícia, a Nestlé incorporou o Seiso em suas fábricas de chocolate. Antes, era comum encontrar pequenos resíduos de produção acumulados ao longo do tempo. Com o Seiso, a limpeza passou a ser parte integral da rotina de cada turno, e isso não apenas melhorou a higiene, mas também aumentou a vida útil dos equipamentos em cerca de 10%.
Seiketsu (Padronização): Criando regras para manter a ordem

Depois de organizar e limpar, o próximo passo é garantir que essas práticas sejam mantidas. Seiketsu se refere à padronização, ou seja, criar regras e procedimentos claros para que o ambiente organizado e limpo não volte ao estado caótico.
- Exemplo na prática: A General Electric implementou o Seiketsu em suas fábricas, criando procedimentos padronizados para inspeção e limpeza de máquinas. Eles desenvolveram guias visuais e checklists para cada setor da linha de produção, o que garantiu que todos os trabalhadores seguissem os mesmos padrões. Isso resultou em uma melhoria de 18% na eficiência geral da produção.
- Outro exemplo: Na área de tecnologia, a Google usa Seiketsu para padronizar seus espaços de trabalho. Cada estação de trabalho é configurada de forma semelhante em todos os escritórios globais da empresa, o que permite que os funcionários trabalhem em qualquer local sem precisar se adaptar a um novo ambiente. Isso padroniza não só o espaço físico, mas também os processos de trabalho.
Shitsuke (Disciplina): Mantendo o 5S funcionando ao longo do tempo
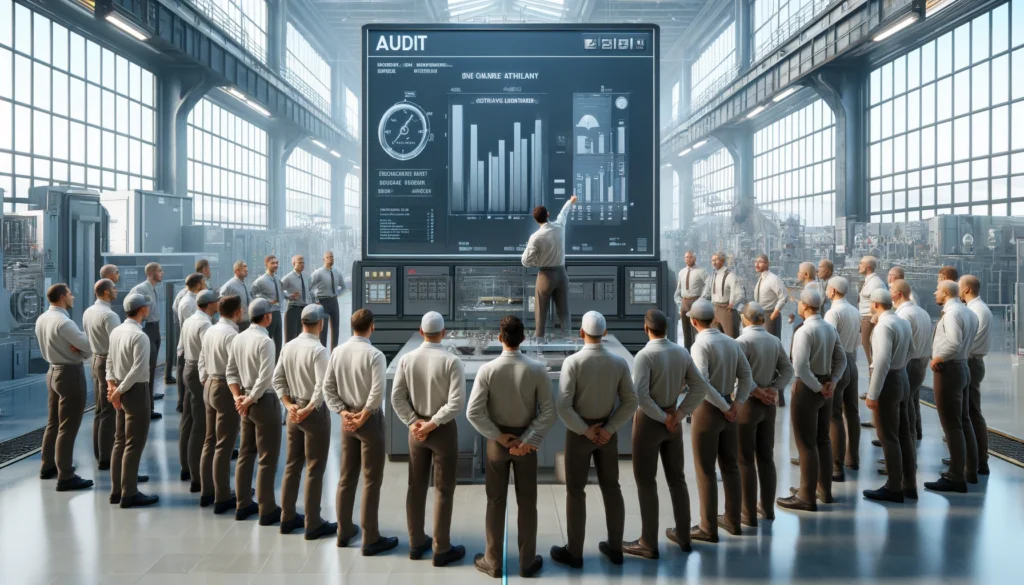
Por fim, a palavra Shitsuke significa “disciplina”. É, talvez, a mais difícil de todas, pois depende de uma mudança cultural dentro da empresa. Ela envolve treinar e educar os funcionários para que sigam os padrões estabelecidos de forma contínua, garantindo que o 5S não seja apenas um projeto temporário, mas uma nova maneira de trabalhar.
- Exemplo na prática: A Honda é conhecida por sua cultura de disciplina e, ao adotar o Shitsuke, ela garantiu que todos os níveis hierárquicos da empresa fossem responsáveis por manter os padrões do 5S. A empresa criou um sistema de auditorias regulares, onde cada setor é avaliado mensalmente. Os funcionários são incentivados a se autoavaliar e a sugerir melhorias. Esse foco em disciplina garantiu que o 5S fizesse parte do DNA da empresa, resultando em uma produtividade 15% maior na última década.
- Outro exemplo: Na DHL, a disciplina do Shitsuke é mantida através de programas de incentivo para os funcionários que seguem os padrões de organização e limpeza estabelecidos pelo 5S. A empresa implementou um sistema de recompensas, onde equipes que mantêm os padrões de excelência por seis meses consecutivos são reconhecidas publicamente. Isso não só garante a longevidade do 5S, mas também motiva os funcionários a manterem a disciplina.
Mas por que tantas empresas adotam essa metodologia?
A implementação do 5S vai muito além de criar um ambiente mais organizado e limpo. Segundo dados da Association for Manufacturing Excellence (AME), empresas que aplicaram o 5S viram um aumento médio de 30% na eficiência operacional nos primeiros seis meses. Mas esse número pode variar dependendo do setor. Na indústria automobilística, empresas como Ford e General Motors relataram reduções de até 50% no tempo de setup de máquinas, enquanto na área de saúde, hospitais que adotaram o 5S, como o Hospital Israelita Albert Einstein, conseguiram diminuir em 20% o tempo de atendimento aos pacientes.
Resultados reais em empresas reais: o impacto global do 5S
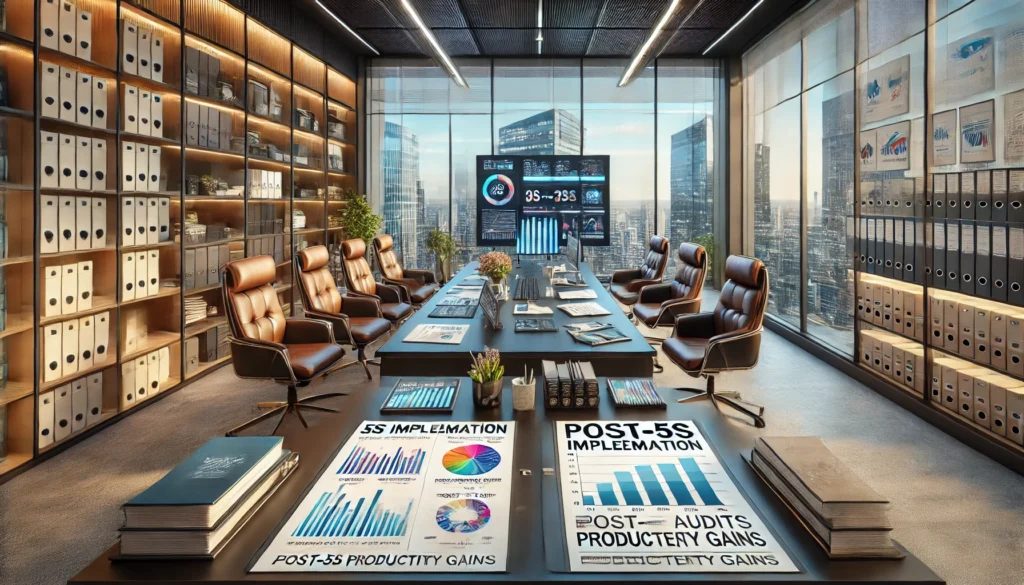
O impacto do 5S não se limita a fábricas e indústrias. Até grandes corporações de tecnologia, como a Microsoft e a Samsung, adotaram essa metodologia em áreas de desenvolvimento e pesquisa, o que resultou em maior eficiência na gestão de projetos e até na aceleração do lançamento de novos produtos.
Na Nestlé, por exemplo, a implementação do 5S em sua fábrica de chocolates na Suíça resultou na eliminação de 15% dos desperdícios de produção em apenas um ano. O segredo? A prática contínua da metodologia aliada à tecnologia. Eles implementaram checklists digitais que permitem que os funcionários acompanhem em tempo real a organização e limpeza dos postos de trabalho.
Manter o ritmo: checklists e auditorias

É claro que implementar o 5S é apenas o começo. O grande desafio é garantir que ele seja mantido ao longo do tempo. É aqui que entram as auditorias regulares, um ponto crucial para garantir a sustentabilidade do sistema. Empresas como a Honda realizam auditorias mensais, onde a equipe de qualidade verifica o cumprimento de cada um dos 5S. Para facilitar, muitas organizações estão utilizando ferramentas online, como o Trello ou o Microsoft Teams, que permitem a criação de checklists dinâmicos e o acompanhamento em tempo real do progresso das equipes.
Empresas mais avançadas na aplicação do 5S, como a Johnson & Johnson, estão investindo em dashboards digitais, onde cada linha de produção é monitorada quanto à eficiência, limpeza e organização. Esses painéis permitem que os gestores identifiquem rapidamente onde está o gargalo e o que precisa ser corrigido.
E os desafios? Nem tudo são flores
Apesar de todo o sucesso, há polêmicas em torno do 5S. Alguns críticos apontam que a metodologia pode ser difícil de implementar em culturas organizacionais mais rígidas ou hierárquicas. Na década de 1990, a Volkswagen enfrentou resistência ao tentar aplicar o 5S em algumas de suas fábricas na Alemanha, devido à forte cultura sindical que priorizava outras formas de melhoria de produtividade. A empresa acabou optando por uma implementação mais gradual, combinando o 5S com outras iniciativas de melhoria contínua, como o Kaizen.
Além disso, algumas empresas relataram que o 5S pode se tornar um processo cansativo se não houver uma verdadeira mudança cultural. O sucesso depende, em grande parte, da mentalidade dos colaboradores e da liderança. Um exemplo negativo foi o da Sony na década de 2000, quando tentaram aplicar o 5S em suas fábricas na China, mas não conseguiram manter a disciplina a longo prazo, resultando em uma reversão nos ganhos de eficiência.
Por que você deveria considerar o 5S?
Seja em grandes corporações globais ou em pequenas empresas familiares, o 5S tem o potencial de transformar o dia a dia das operações. Seus resultados são claros: mais produtividade, menos desperdício e um ambiente de trabalho muito mais agradável. Mais do que uma ferramenta de organização, o 5S promove uma verdadeira revolução cultural dentro das organizações, mudando a forma como as pessoas enxergam o local onde trabalham.
E o mais interessante: a metodologia não é exclusiva de fábricas. Escritórios, hospitais, escolas, qualquer lugar que precise de organização pode aplicar o 5S. Afinal, quem não gostaria de trabalhar em um ambiente mais limpo, organizado e eficiente?
O sucesso está nos detalhes, e como vimos, o 5S é uma ferramenta poderosa para transformar o caos em ordem – e fazer com que essa ordem dure ao longo do tempo.